
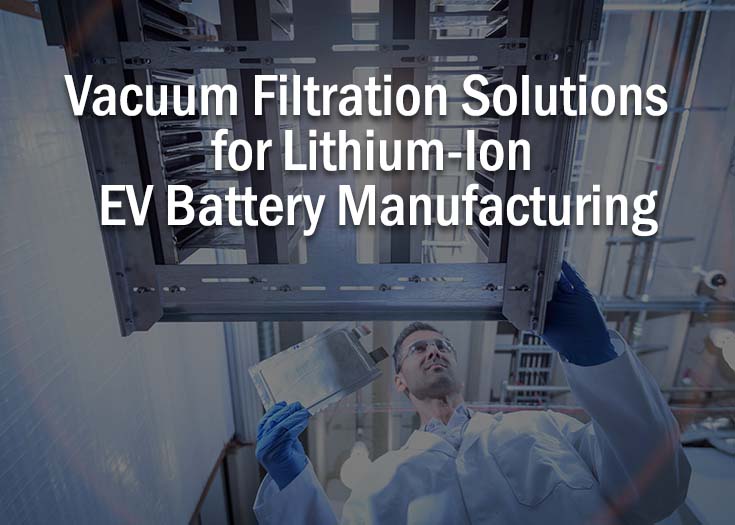
Introductie
De globale markt voor de productie van oplaadbare (secundaire) lithium-ion batterijen blijft groeien als gevolg van de explosieve vraag naar elektrische voertuigen (EVs) onder invloed van het overheidsbeleid en veranderend consumentengedrag. Daarnaast is energieopslag uit hernieuwbare energiebronnen (zon en wind) de volgende stap voor lithium-ion batterijen.
Er worden drie veel voorkomende li-ion celontwerpen gebruikt voor de productie van EVs, energieopslag en consumentenelektronica (telefoons, laptops, etc.), namelijk pouch celbatterijen, prismatische celbatterijen en cilindrische celbatterijen .
Pouch celbatterijen
Het omhulsel (lijkend op een foliezakje) van pouch celbatterijen is licht, compact en zorgt voor de beste vermogensafgifte en efficiëntie.Het foliezakje is echter gevoeliger voor beschadiging dan andere typen lithium-ion batterijen met een stevig omhulsel. Desondanks zorgt de combinatie van grootte, prestaties en efficiëntie ervoor dat pouch celbatterijen de nieuwste standaard zijn voor EVs.

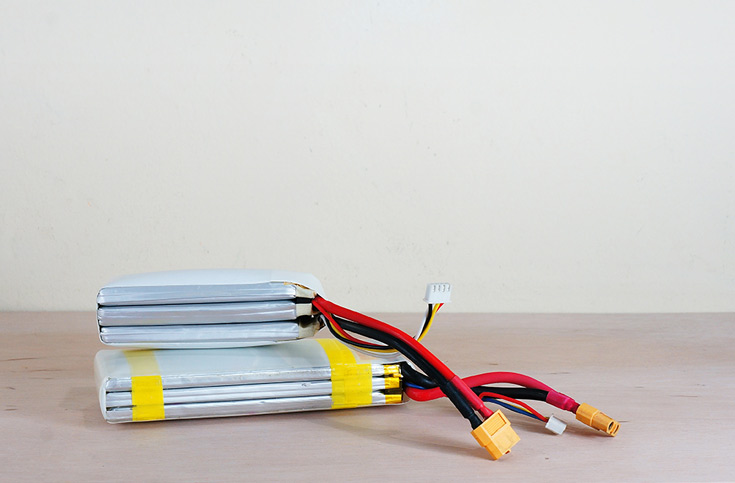
Prismatische celbatterijen
Stevige aliumnium of stalen externe behuizingen zijn de traditionele standaard voor consumentenelektronica en EVs. Hoewel prismatische celbatterijen een robuustere constructie kennen dan de pouch celbatterijen, zijn de stijve verpakking en het grotere formaat nadelig.

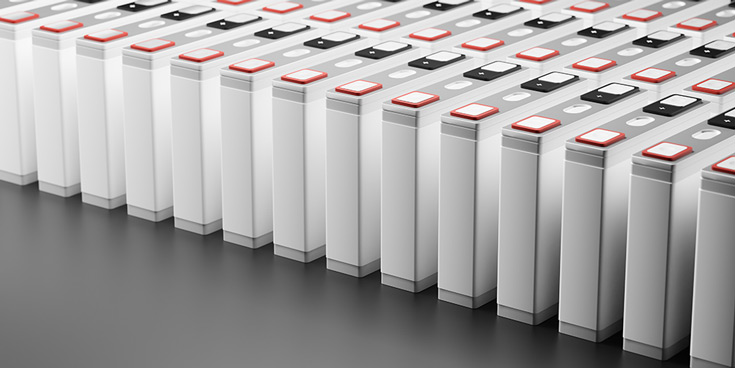
Cilindrische celbatterijen
Met hun vaste vorm en stevige metalen behuizing zijn cilindrische celbatterijen het minst duur en werden ze vooral gebruikt voor de eerste generatie EVs. De vaste vorm, het formaat en het gewicht zijn echter nadelig voor de prestaties in vergelijking met de pouch celbatterijen of prismatische celbatterijen.
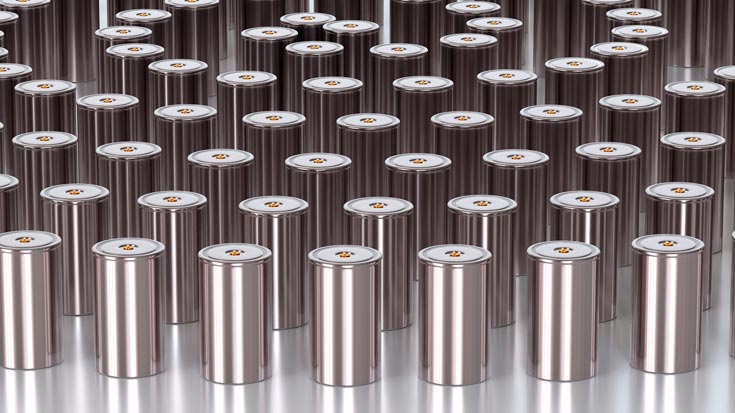
Vacuüm is een integraal onderdeel tijdens de meeste fasen van het productieproces van batterijen waaronder het pneumatisch transport van grondstoffen, het mengen van elektrodeslurry, het vullen van elektrolyten, het ontgassen en de uiteindelijke afdichting van het complete EV batterijpakket. In elke fase helpt vacuüm de zuiverheid, precisie en consistentie van het materiaal te behouden wat wederom resulteert in een verbetering van batterijvermogen, energiedichtheid, levensduur en laadsnelheid. Tegelijkertijd veroorzaakt elk proces verontreinigingen (deeltjes, vloeistoffen en dampen) die in de vacuümpomp kunnen terechtkomen. Speciaal ontworpen filtratieoplossingen vangen verontreinigingen op, beschermen de vacuümpomp, verlagen de onderhoudskosten en bevorderen de uptime in de huidige 24/7 industrie.
In our blog, we will focus on three primary manufacturing processes (Electrode Manufacturing, Cell Assembly, and Cell Finishing), how vacuum is used within each, and the recommended filtration solutions.
Productie van elektroden
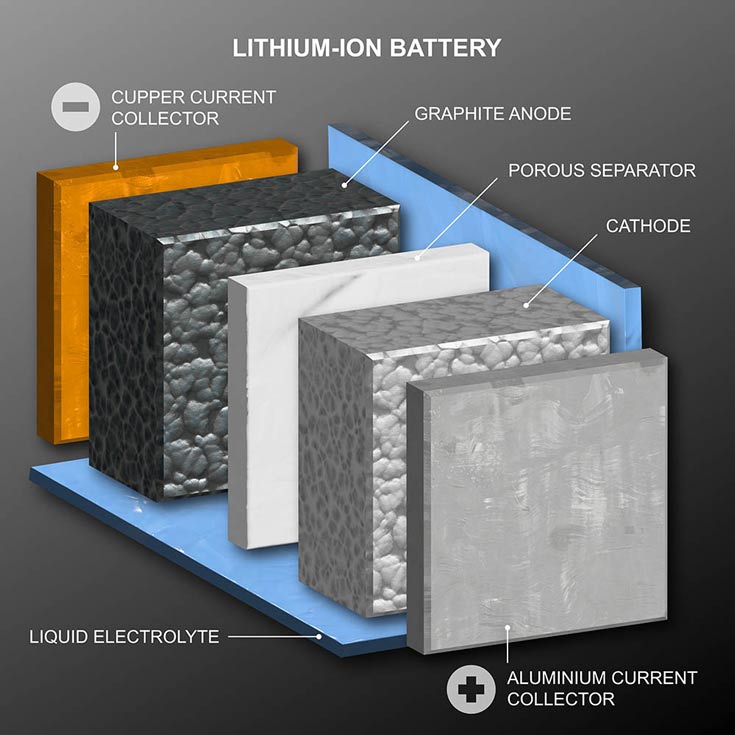
Voorafgaand aan de productie worden grondstoffen gewonnen en verwerkt tot een verfijnde poedervorm.
Vacuümpompen en blowers worden gebruikt voor het pneumatisch transport van materialen zoals lithium, grafiet, kobalt en mangaan. Zodra de materialen beschikbaar zijn, is de eerste stap het maken van de elektroden (kathode en anode) die cruciaal zijn voor de uitwisseling van lithiumionen. Bij het mengen van elektrodeslurry worden droge materialen gecombineerd, met name actieve materialen (zie hieronder)*, geleidende additieven (roet), bindmiddelen en oplosmiddelen (gedeïoniseerd water voor de anode en N-methylpyrrolidon (NMP) voor de kathode). Er wordt vacuüm gebruikt om luchtbellen te verwijderen en een homogene slurry te bekomen, hetgeen cruciaal is voor de efficiëntie en prestaties van de elektrode.
*Actieve materialen
Anode
- Er wordt voornamelijk gebruik gemaakt van grafiet
- Silicone wordt gebruikt in de nieuwere generaties vanwege de hogere capaciteit en energiedichtheid
Kathode
- Lithiumkobaltoxide (LiCoO2)
- Lithium mangaanoxide (LMnO2)
- Lithium nikkel oxide (LiNiO2)
De uiteindelijke slurry wordt gebruikt om geleidende metalen stroken van aluminium of koper te coaten. De stroken worden gedroogd door middel van warmte om het resterende NMP oplosmiddel af te scheiden en terug te winnen voordat de stroken worden samengeperst/afgevlakt en gereinigd, gesneden/geslepen en verwerkt tot rollen. De rollen ondergaan een laatste vacuümdroogproces om eventueel resterende oplosmiddelen en vocht te verwijderen. Het elektrodemateriaal wordt nu opgeslagen in een droge ruimte voor lokale celassemblage of vacuüm verpakt voor gebruik door andere celfabrikanten.
Technologieën voor zowel oliegesmeerde als droge vacuümpompen worden regelmatig ingezet voor meng- en droogprocessen. Voor beide types is inlaatfiltratie van cruciaal belang voor de bescherming van apparatuur tegen verontreinigingen en het voorkomen van verminderde vacuümprestaties en storingen.
Filtratie oplossingen bij pneumatisch transport van grondstoffen
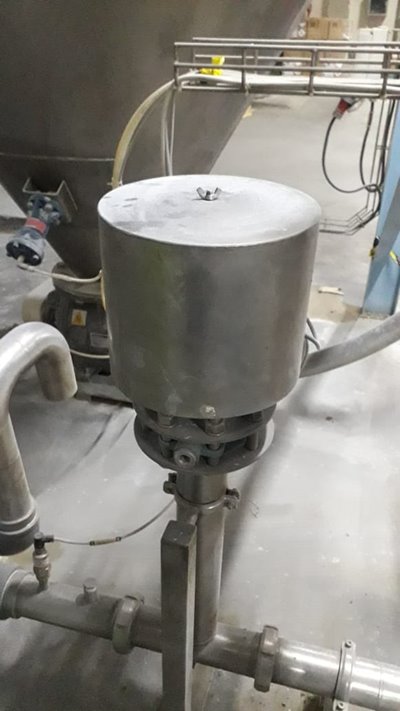
Inlaatfilters, filtergeluidsdempers en ventilatiefilters
- Vanwege de zuiverheidseisen aan grondstoffen moet de lucht die nodig is voor het transport via druk of vacuüm worden gefilterd. Inlaatfilters en filtergeluidsdempers zoals de Solberg F, FS en 2G Serie vangen omgevingsverontreinigingen op en verminderen tegelijkerheid het geluid van de inlaatlucht.
- Aangezien deze systemen in cleanrooms worden geïnstalleeerd, moet stof uit de ventilatieopeningen worden opgevangen om omliggende fabrieksruimten en operators te beschermen.
- De micronwaarde en efficiëntie van de interne filterelementen moeten worden afgestemd op de specifieke systeemvereisten: 99+% efficiënt voor deeltjes van 5 of 1 micron ofhoog efficiënt H14/ULPA classificatie 99.995% efficiënt voor deeltjes van 0.1 micron.
Inlaatvacuümfilters
- Een vacuümpomp of blower vereist een uiterst efficiënte filtratie om de fijne stofdeeltjes op te vangen die stroomopwaartse stofafscheiders omzeilen.
- Inline vacuümfilters zoals de Solberg CSL, CSS en ST Serie dienen als laatste verdedigingslinie voor de vacuümpomp of blower.
Vacuümfiltratie oplossingen bij productie van elektroden
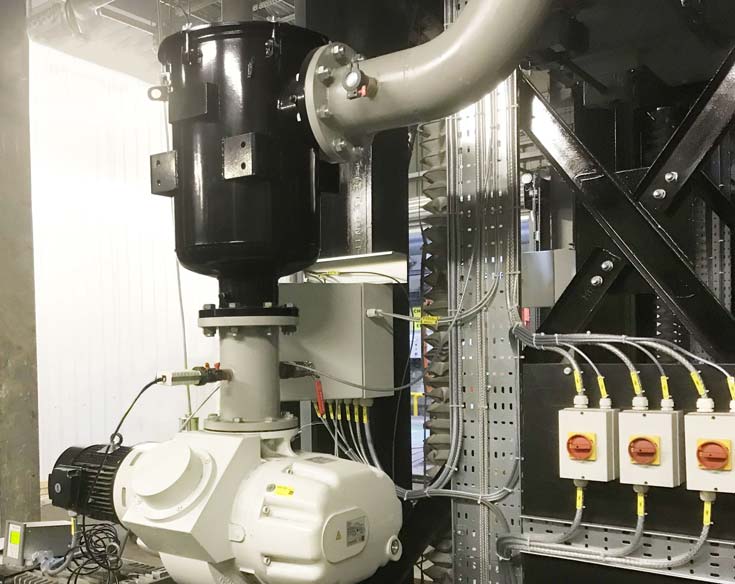
Heavy duty inlaatvacuümfilters
- Bij het toepassen van vacuüm tijdens het meng- en droogproces zullen deeltjes naar de vacuümpomp worden gezogen. Daarom zijn deeltjesfilters zoals uit de CSL, ST, en WL Serie nodig om pompvervuiling te voorkomen.
- Het interne filterelement, de micronwaarde en de efficiëntie worden geselecteerd op basis van de specifieke bedrijfsomstandigheden van het productieproces van de Li-Ion batterij. Polyester van 5 micron (99+% efficiënt) presteert in de meeste gevallen goed. Andere filtermedia, micronwaardes en efficiënties zijn beschikbaar afhankelijk van de specifieke procesomstandigheden. .
- Er zijn verschillende constructiematerialen (koolstofstaal, roestvrijstaal, enz. ) en aansluittypes (DN flenzen, ANSI flenzen, ISO-K flenzen) verkrijgbaar, afhankelijk van de procesleidingen en vacuümpompaansluitingen.
- Routineonderhoud omvat het reinigen en eventueel vervangen van de interne filterelementen.
Dampcondensatiefilters voor:
- Dampcondensatie onder vacuüm is een uitdaging vanwegen de dampdruk van NMP en water. Het is wel uiterst belangrijk voor oliegesmeerde pompen die worden gebruikt voor de productie van elektroden omdat de olie kan emulgeren wanneer dampen in de olie condenseren.
- Een meertraps condensatiefilter zoals uit de Solberg JRS Series or JCT Series, werkt in combinatie met een door de fabriek geleverde gekoelde vloeistofbron (glycol, water) om een koud oppervlak te creëren voor het condenseren van dampen. De vereiste vloeistoftemperatuur is afhankelijk van de specifieke procesomstandigheden.
- Het interne koeloppervlak van de JRS of JCT is een gepatenteerd roestvrijstalen geplooid plissépakket dat is ontworpen om het oppervlak te maximaliseren waardoor de prestaties van traditionele koelspiraalontwerpen worden overtroffen. Door de juiste dimensionering wordt de verblijftijd op het koeloppervlak gemaximaliseerd wat de condensatieprestaties verbetert.
- Meerdere filtratiefasen zullen de filtratie efficiëntie verhogen. Daarom zijn roestvrijstalen demisterpads een veelgebruikte tweede trap om gecondenseerde druppels af te scheiden en zijn uiteindelijk actieve kool adsorptiefilterelementen ideaal om in een laatste trap restdampen op te vangen.
- Er moet rekening gehouden worden met verschillende constructiematerialen (koolstofstaal, roestvrijstaal, etc) en aansluitingen (DN flenzen, ANSI flenzen, ISO-K flenzen) om de procesomstandigheden aan te kunnen en te passen binnen de beschikbare ruimte op of nabij de vacuümpompen.
- Filtration experts will specify a filter size, cooling surface area, and chilled fluid requirements depending on the process flow, operating vacuum level, operating temperature, and chemistry.
Door de vacuümapparatuur te beschermen met een speciaal ontworpen inlaatfiltratieoplossing tijdens het productieproces van elektroden zal de operator langere onderhoudsintervalllen en lagere onderhoudskosten bereiken.
Celassemblage
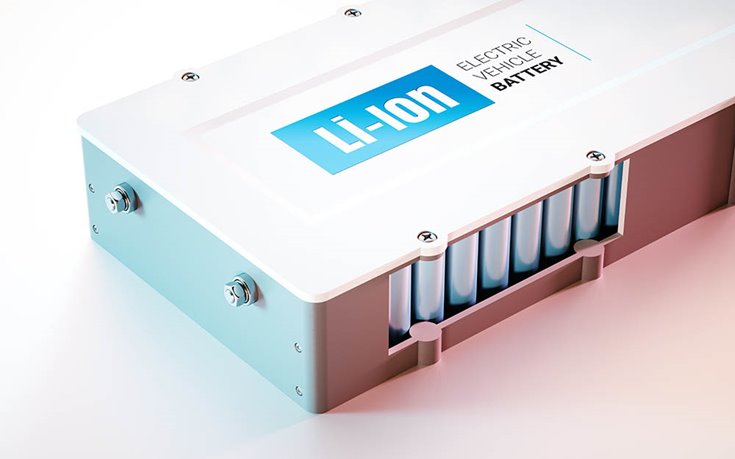
Het gedroogde elektrodemateriaal wordt gesneden en vervolgens samen met scheidingsmateriaal in lagen gestapeld om de kern van de cel te vormen.
Het scheidingsmateriaal vormt een noodzakelijke barrière tussen de anode en de kathode en zorgt tegelijkertijd voor een continue uitwisseling van lithiumionen tijdens het ontladen en opladen.
De lagen wisselen anode-scheidingsmateriaal-kathode-scheidingsmateriaal, enzovoort af. De celstructuur wordt vervolgens ultrasoon gelast aan de aansluitingen die uiteindelijk de elektrische stroom zullen leiden.Voor de huidige EVs geldt de pouch celbatterij als standaard vanwege de lagere profielvorm, het compacte formaat, het lichtere gewicht, de flexibiliteit en de sterkte. De celkern wordt in de met aluminium beklede polymeerfolie geplaatst en aan drie zijden afgedicht waardoor er één opening over blijft voor het toekomstige elektrolytvulproces.
Bij prismatische en cilindrische celbatterijen worden de lagen opgerold en vervolgens verpakt in een robuust metalen omhulsel. Tijdens deze fase worden de aansluitingen ultrasoon gelast en wordt het omhulsel vervolgens eveneens afgedicht met laser of ultrasoonlassen. Op dit punt worden de cellen voorbereid op het elektrolytvulproces.
Elektrolytvullen vindt plaats wanneer het mengsel van lithiumzout in een organische oplossing (hexafluorfosfaat LiPF6) in de celstructuur wordt geïnjecteerd. De elektrolyt bevordert de stroom van lithiumionen van de anode naar de kathode tijdens het ontladen van de batterij en van de kathode naar de anode tijdens het opladen van de batterij. Bij het vullen van prismatische of cilindrische celbatterijen wordt een doseernaald via een klep/fitting ingebracht. Het vullen gebeurt onder vacuüm omwille van twee belangrijke redenen:
- Vacuüm evacueert de cel om lucht en onzuiverheden te verwijderen
- Vacuüm bevordert het capillaire effect (bevochtiging) en de gelijkmatige verdeling van het elektrolytmengsel door de cel
- Zodra het vullen voltooid is, wordt de verpakking doorgaans verzegeld door lassen
Bij een pouch celbatterij zorgt de resterende opening voor toegang van de doseernaald om te vullen.
Ook hier vindt de vulling onder vacuüm plaats om het capillaire effect te bevorderen. Eens gevuld, wordt het zakje vacuümverzegeld. Hierna kan de afwerkingsfase beginnen.
Vacuümfiltratie oplossingen bij celassemblage
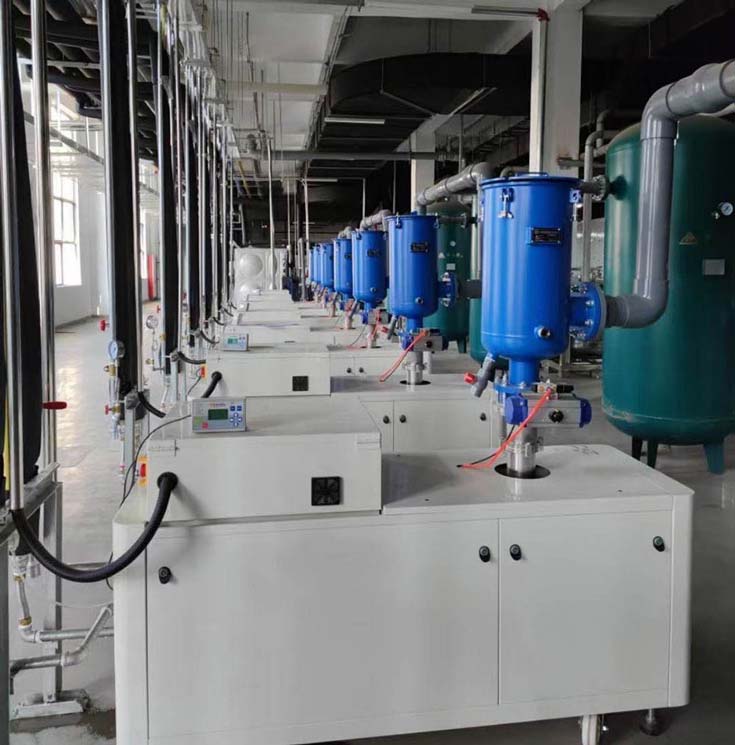
Vloeistofafscheiders
- Wanneer de cel onder vacuüm wordt gevuld, zal er een beetje elektrolytoplossing naar de pomp worden gezogen wat een vloeistofafscheider ideaal maakt om pompverontreiniging te voorkomen.
- Een meertraps vloeistofascheider zoals de Solberg LRS Series is een afscheider met lage snelheid en een hoog rendement om de elektrolyt op te vangen. .
- Interne baffle voor een eerste afscheiding
- Bodemkamer voor vloeistofopvang
- Filterelement als laatste fase om eventueel achtergebleven vloeistofdruppels en zwevende deeltjes op te vangen.
Er wordt rekening gehouden met verschillende constructiematerialen (koolstofstaal, roestvrijstaal, etc) en aansluitingen (DN flenzen, ANSI flenzen, ISO-K flenzen) om de procesomstandigheden aan te kunnen en te passen binnen de beschikbare ruimte op of nabij de vacuümpompen.
Dampcondensatiefilters voor vacuümtoepassingen
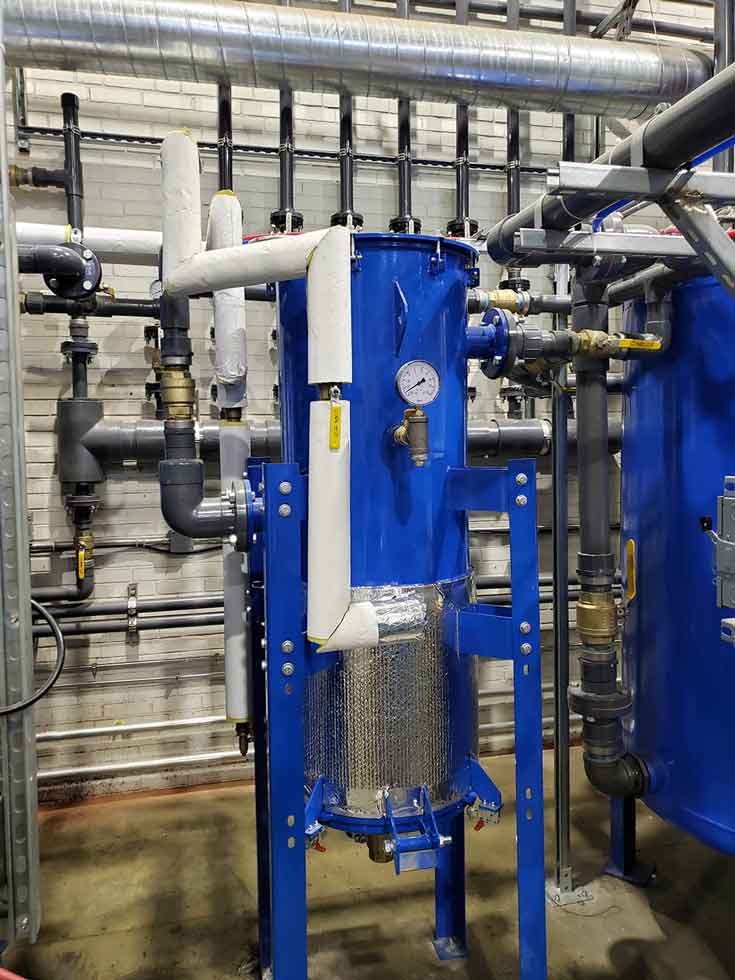
- Dampcondensatie onder vacuüm is een uitdaging vanwege de dampdruk van de elektrolyt. Dit is vooral belangrijk bij oliegesmeerde pompen omdat de olie kan emulgeren wanneer dampen in de olie condenseren.
- Een meertraps condensatiefilter zoals de Solberg JRS Series or JCT Series werkt in combinatie met een door de fabriek geleverde gekoelde vloeistofbron (glycol, water) om een koud oppervlak te creëren voor het condenseren van dampen. De vereiste vloeistoftemperatuur is afhankelijk van de specifieke procesomstandigheden.
- Het interne koeloppervlak van de JRS of JCT is een gepatenteerd roestvrijstalen geplooid plissépakket dat is ontworpen om het oppervlak te maximaliseren waardoor de prestaties van traditionele koelspiraalontwerpen worden overtroffen.
- Door de juiste dimensionering wordt de verblijftijd op het koeloppervlak gemaximaliseerd wat de condensatieprestaties verbetert.
- Meerdere filtratiefasen zullen de filtratie efficiëntie verhogen. Daarom zijn roestvrijstalen demisterpads een veelgebruikte tweede trap om gecondenseerde druppels af te scheiden en zijn adsorptiefilterelementen ideaal om in een laatste trap restdampen op te vangen.
- Er moet rekening gehouden worden met verschillende constructiematerialen (koolstofstaal, roestvrijstaal, etc) en aansluitingen (DN flenzen, ANSI flenzen, ISO-K flenzen) om de procesomstandigheden aan te kunnen en te passen binnen de beschikbare ruimte op of nabij de vacuümpompen.
Voor het vullen van elektrolyten bepalen filtratie experts de grootte van het filter, het koeloppervlak en de vereisten voor de gekoelde vloeistof rekening houdend met de processtroom, het bedrijfsvacuüm, de bedrijfstemperatuur en de chemische samenstelling van de applicatie.
Celafwerking
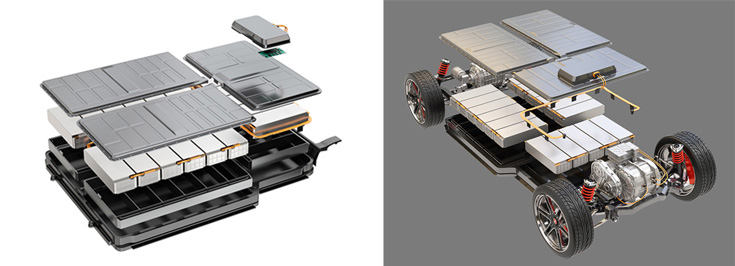
Ongeveer een derde van de productietijd wordt besteed aan de afwerkingsfase die drie primaire processen omvat: vorming, veroudering en testen. Tijdens de vormingsfase ontvangt de cel zijn eerste lading en wordt de cel vervolgens ontladen en opgeladen op basis van specifieke parameters. Lithiumionen zijn ingebed in grafietkristallen van de anode waardoor een beschermende laag ontstaat tussen de elektrode en de elektrolyt – de zogenaamde Solid Electrolyte Interface (SEI).Deze laag is van cruciaal belang om zelfontlading van de batterij te voorkomen. Het snelladen resulteert in reacties tussen de elektrolyt en de elektroden. De resulterende giftige gassen (C2H4, C02, CO, H2) worden uit de pouch cel naar een aangrenzende gaszak geduwd.
In een vacuümkamer wordt deze gaszak doorboord, worden gassen afgescheiden en wordt de zak vervolgens vacuümverzegeld. Bij een prismatische cel wordt de cel zelf doorboord en worden de gassen via vacuüm afgescheiden. De cel wordt vervolgens opnieuw afgedicht om te voorkomen dat verontreinigingen in de cel terechtkomen en om veiligheidsproblemen, een kortere levensduur van de cel en prestatieverlies te vermijden.
Zodra het ontgassen is voltooid, worden de cellen dagen- en wekenlang “verouderd” en worden de prestaties gecontroleerd. Als er geen degradatie optreedt, zijn de cellen klaar voor een laatste lektest voordat ze in een batterijpakket worden geïnstalleerd. Het testen van harde cellen gebeurt meestal in een vacuümkamer met instrumenten die eventuele elektrolytlekken kunnen opsporen. Pouch cellen kunnen ook worden getest op elektrolytlekken maar hiervoor moet een speciale procedure en kamer worden gebruikt aangezien de cellen gemakkelijk kunnen uitzetten of beschadigd raken onder vacuüm.
Vacuümfiltratie oplossingen bij celafwerking
Heavy duty inlaatvacuümfilters
- Deeltjesfilters zoals de Solberg CSL, ST, and WL zijn speciaal ontwerpen voor het verwijderen van verontreinigingen en het afdichten tijdens de celafwerkingsfase.
- Het interne filterelement, de micronwaarde en de efficiëntie worden geselecteerd op basis van de specifieke bedrijfsomstandigheden. Polyester van 5 micron (99+% efficiënt) presteert in de meeste gevallen goed. Andere filtermedia, micronwaardes en efficiënties zijn beschikbaar afhankelijk van de specifieke procesomstandigheden.
- Voor ontgassing kan de CSL of WL worden uitegrust met een adsorptief filterelement om dampen op te vangen die tijdens de vormingsfase ontstaan.
- Er zijn verschillende constructiematerialen (koolstofstaal, roestvrijstaal, enz. ) en aansluittypes (DN flenzen, ANSI flenzen, ISO-K flenzen) verkrijgbaar, afhankelijk van de procesleidingen en vacuümpompaansluitingen.
- Routineonderhoud omvat het reinigen en eventueel vervangen van de interne filterelementen.
Conclusie
De explosieve wereldwijde vraag naar lithium-ionbatterijen zal de investeringen in aanvullende apparatuur die nodig is voor de productie van elektroden, celassemblage en celafwerking blijven stimuleren. Het transporteren van grondstoffen, het mengen van slurry, het vullen van elektrolyten, het ontgassen en andere processen vereisen allemaal vacuüm. Gezien de verfijning en precisie van de huidige vacuümpompen is bescherming nodig om verontreinigingen in de vorm van deeltjes, vloeistoffen en dampen op te vangen. Rekening houden met het 24/7 karakter van de industrie en het feit dat de meeste batterijfabrieken op (bijna) 100% capaciteit draaien is er geen marge voor downtime en productieverlies. Speciaal ontworpen vacuümfiltratieoplossingen beschermen de pompen en zorgen ervoor dat ze continu en efficiënt kunnen werken wat maximale batterijproductie en -prestaties mogelijk maakt.
De wereldwijde industriële partnerschappen van Solberg op het gebied van de productie van lithium-ionbatterijen, huidige klanten en projectervaringen geven ons een duidelijk beeld in de verschillende vacuümprocesomstandigheden. We bieden technisch advies aan toonaangevende fabrikanten van apparatuur, OEMs van vacuümpompen, servicebedrijven en strategische eindgebruikers om te laten zien op welke manier hoogefficiënte filtratie de uptime en productieoutput van vacuümapparatuur maximaliseert en tegelijkertijd kostbare revisies en onderhoud vermindert.